Sheet Metal Fabrication
OTHER SERVICES
Sheet Metal Fabrication
Download our Brochure
Our company profile
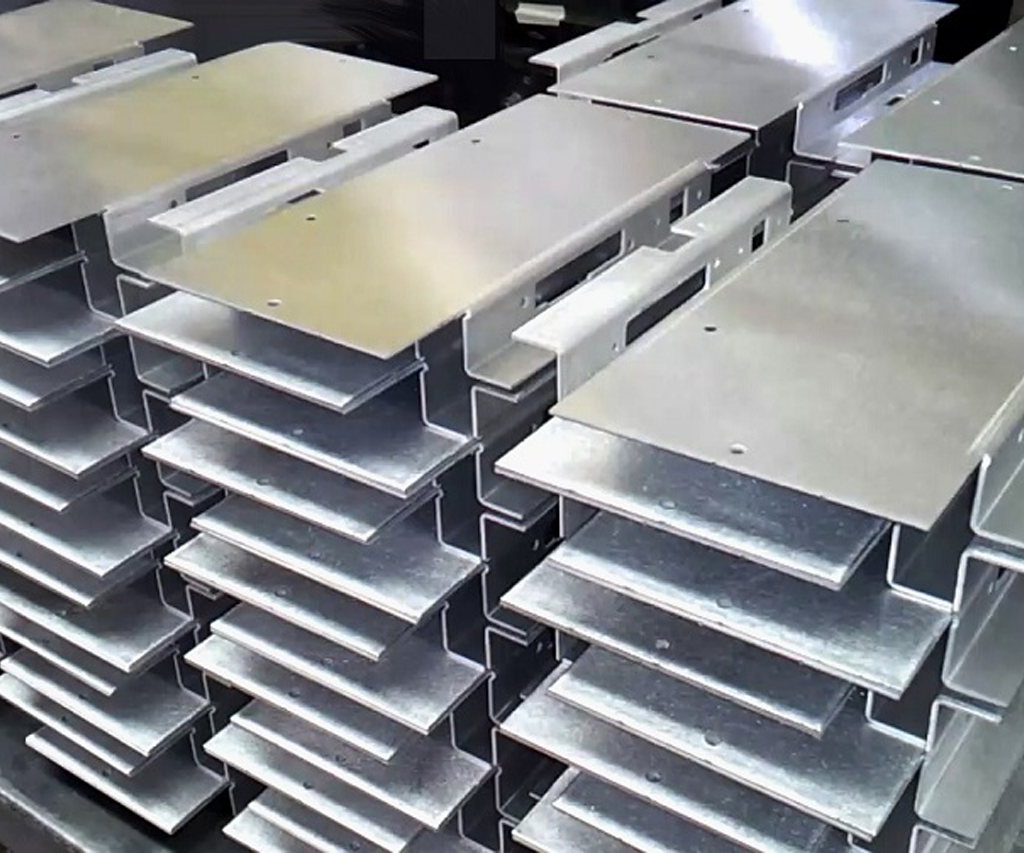
CONTACT US TODAY
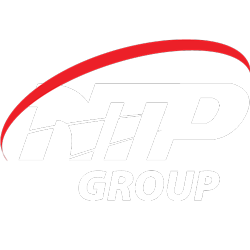
Vo Quy
Sales Manager VIETNAM
+84 982998709
Brett McMiles
Business Development / Sales Manager INTERNATIONAL
+61 428887392
Sheet Metal Fabrication Process
Sheet metal fabrication is any process that involves assembling or manufacturing raw sheet metal. One or more fabrication processes can be used to produce the desired part, depending on the material and specifications of the project. Clients can choose from metal cutting, welding, bending, machining, punching, and stamping fabrication techniques to create their products. We will explore each metal fabrication technique to help you determine the ideal method(s) for your application.
Metal Stamping.
Metal Welding.
Metal Machining.
Metal Cutting.
Metal Bending (forming).
Metal Punching.
Our Machines
Kruman CLS3216-NC Hydraulic Sheet Shearing
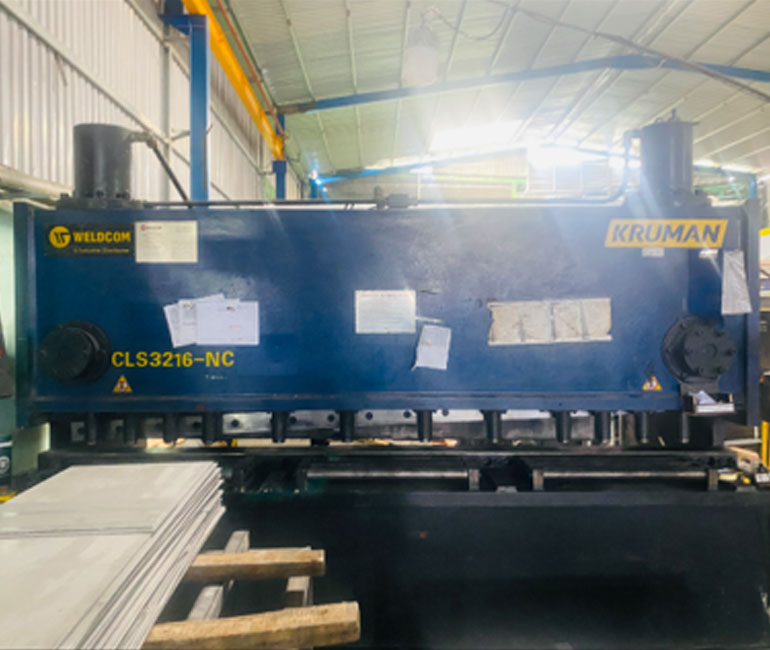
Model: CLS3216-NC
Shearing thickness (mm): 20mm
Shearing width (mm): 3200mm
Shearing angle (°): 0.5-3°
Back gauge range (mm): 20-800mm
Strokes (1/min): 10-20
Main Motor (Kw): 30 Kw
Kruman CYS2506-NC Hydraulic Sheet Shearing
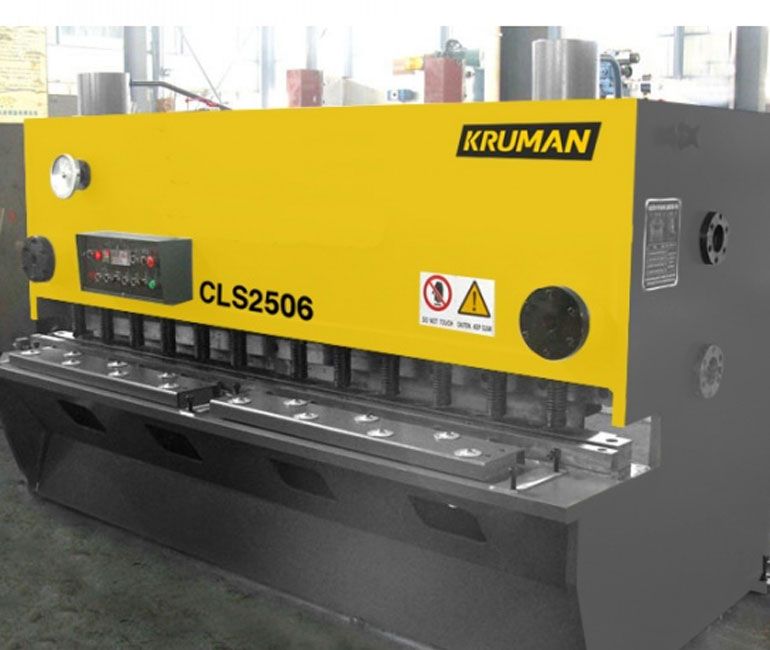
Model: CYS2506-NC
Shearing thickness (mm): 6mm
Shearing width (mm): 2500mm
Shearing angle (°): 0.5-1.5°
Back gauge range (mm): 20-600mm
Strokes (1/min): 16-35
Main Motor (Kw): 7.5Kw
Amada Pega 357 Punch Machine
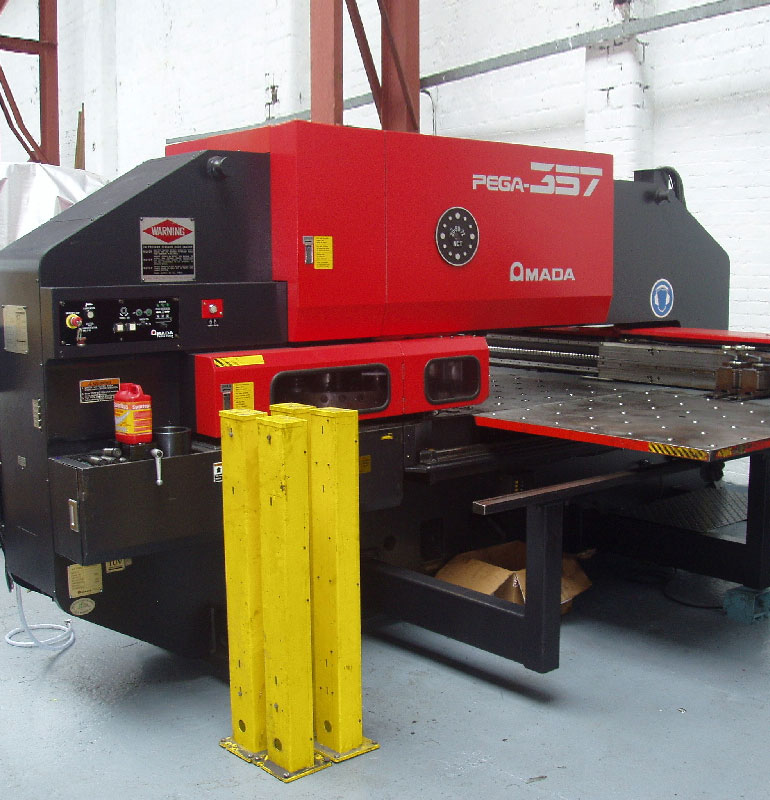
Model: Amada Pega 357, 45 Station Turret with 4 Autoindexing units
Year: 1992
Frame Construction: Bridge Type
Press Capacity: 30 tonnes (294kN)
Axis Traverse Distance: 1270 x 1830mm
Workable Maximum Sheet Size including 1 auto reposition: 1270 x 3660mm
Max. Hole Diameter: 41mm diameter
Max. Material
Max. Material Weight: 100 Kg
Max. Hole Diameter: 114.3mm
No. of Stations: 45 Stations:
24 x A (Max. Dia. 12.7mm),12 x B (Max. Dia. 31.7mm),2 x C (Max. Dia. 50.8mm), 1 x D (Max. Dia. 88.9mm), 2 x E (Max. Dia. 114.3mm), Auto Indexing: 2 x B (Max Dia 31.7mm), 2 x C (Max Dia. 50.8mm)
Axis Speed X/Y: 82 m/min.
Strokes per Minute: 350 S.P.M.
Hits per Minute: 25mm Pitch: 200 H.P.M.
Turret Speed Bi-Directional: 25 RPM
Punching Accuracy: / – 0.1mm ,Ram Stroke Length: 32mm,Axis Drives: AC Servo Motor,Press Motor: 5.5kw
Electric Power Required: 18Kva 400V /- 10% 50Hz
Air Pressure Required: 5.0 Kgf/cm² ,Air Flow : 80 L/min
Machine Length: 5060 mm
Machine Width: 4000 mm
Machine Height: 2400 mm
Machine Weight: 12000 Kg
CNC Pressbrake YAWEI PBH-110/3100
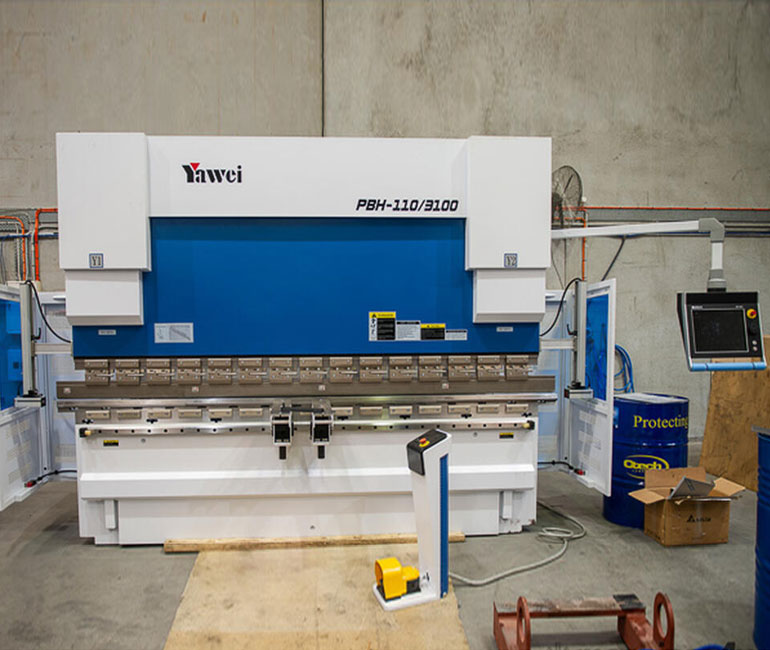
Description: PBH-110–3100-4C
Rated seismic force: 1100KN
Working table length: 3100mmn
Distance between vertical axes: 2600mm
Ram travel: 215mm
Opening height: 520mm
Throat Depth: 410mm
Working speed:
Knife descent: 220 mm/s
Working: 18 mm/s
Tool return: 180 mm/s
Total size:
Length: 3610mm
Width: 1550mm
Height: 2620mm
Oil tank: 300L
Main motor: 12.5KW
Weight: ~8800kg
CNC Pressbrake YAWEI PBH-250/4100
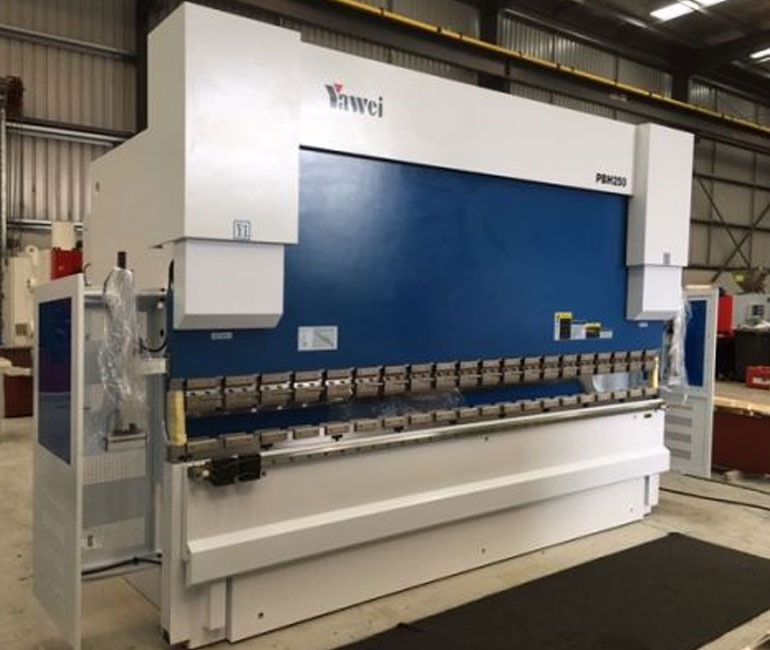
Max force: 2500 KN
Max bending length: 4100mm
Input Voltage: 380V
Phase: 3
Protect grade: IP54
Frequency: 50Hz
Total capacity: 20KvA
Total Breaking current: 63 A
BRUCO BLC SERIES 3000/4000 LIGHT-DUTY CNC CUTTING
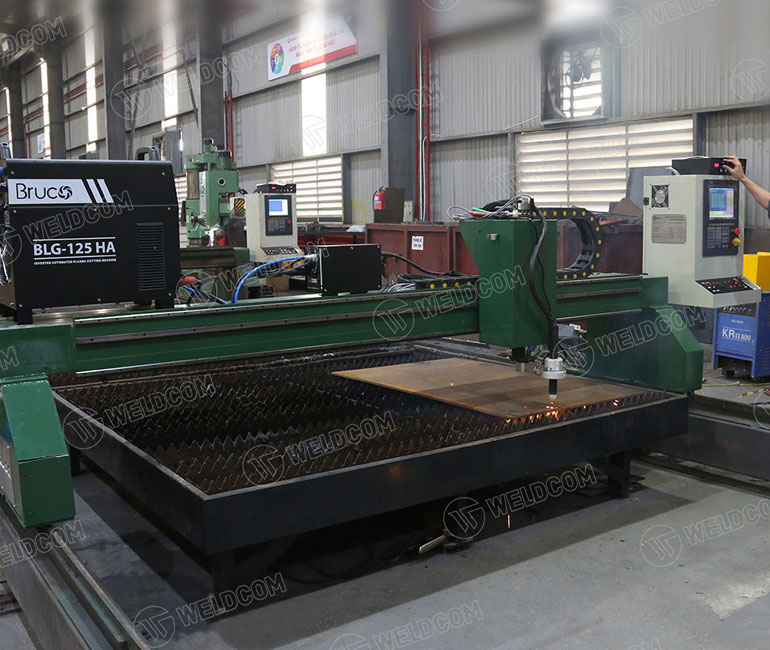
Maximum cutting width: 2,650mm
Maximum cutting length: Depending on rail length
Oxy gas cutting thickness: 6 – 100mm
Plasma cutting thickness: Depending on Plasma source
Distance between 2 rails: 3,000mm
Rail length: Optional
Power source: VAC 220
Engine capacity
(excluding cutting power): kW 3
Frequently Asked Questions
Sheet metal is a flexible construction material with many uses. From mundane things like storage sheds to complex things like aeroplane wings, it can be used for a wide variety of purposes.
There are many distinct types of sheet metal, each with its own advantages and disadvantages. The many types of sheet metal and the applications for each will be discussed.
Sheet metal is an alloy that combines iron with small amounts of other metals like copper, nickel, manganese, or chrome to achieve specific physical properties.
Stainless steel, which resists corrosion better than regular steel, and aluminium, which weighs less but is less durable than other metals, are both options for sheet metal.
Sheet metal can be used for anything from making signs to making automobiles.
What is sheet metal?
Sheet metal is literally that. Large, thin sheets of metal, usually steel or aluminium but sometimes other materials are used. These sheets are thinner than stock bar but thicker than foil and are usually stored in packs, according to their thicknesses.
How thick is sheet metal?
The thickness of the metal sheet can vary, depending on the desired characteristics of the finished product and the processes required during manufacturing. Sheet metal thickness is usually below 6.35mm as processing anything thicker with machines such a turret punch becomes difficult.
What are the processes involved in sheet metal fabrication?
There is a wide range of different processes that make up the sheet metal fabrication process, depending on the required outcome but the most commonly used are:
Sheet metal folding whereby a machined called a press brake applies tonnage of pressure to the sheet to achieve a desired angle.
Sheet metal laser cutting is used to profile a flat metal sheet. The required shape is “nested” onto the sheet using cnc programming and the ultra-high temperature laser machines follows the specified path, piercing through the metal sheet as it goes to leave a cut out shape. Waste sheet metal skeleton is then recycled.
Sheet metal can also be perforated, profiled and formed through a process called punching in which a tool is forced through the sheet at high velocity, causing a perforation. A cnc punch machine will hit the sheet in this way repeatedly at high speed to create the desired pattern.
Sheet metal components are often welded once all other processing has been completed. Components are joined together to form larger assembly’s through a process of MIG, TIG, spot or even robot welding.
Which materials can be processed?
There are many different metals that can be made into sheet metal, such as aluminium, brass, copper, steel, tin, nickel and titanium. Most commonly however, steel, stainless or aluminium sheet metal is chosen for its properties.